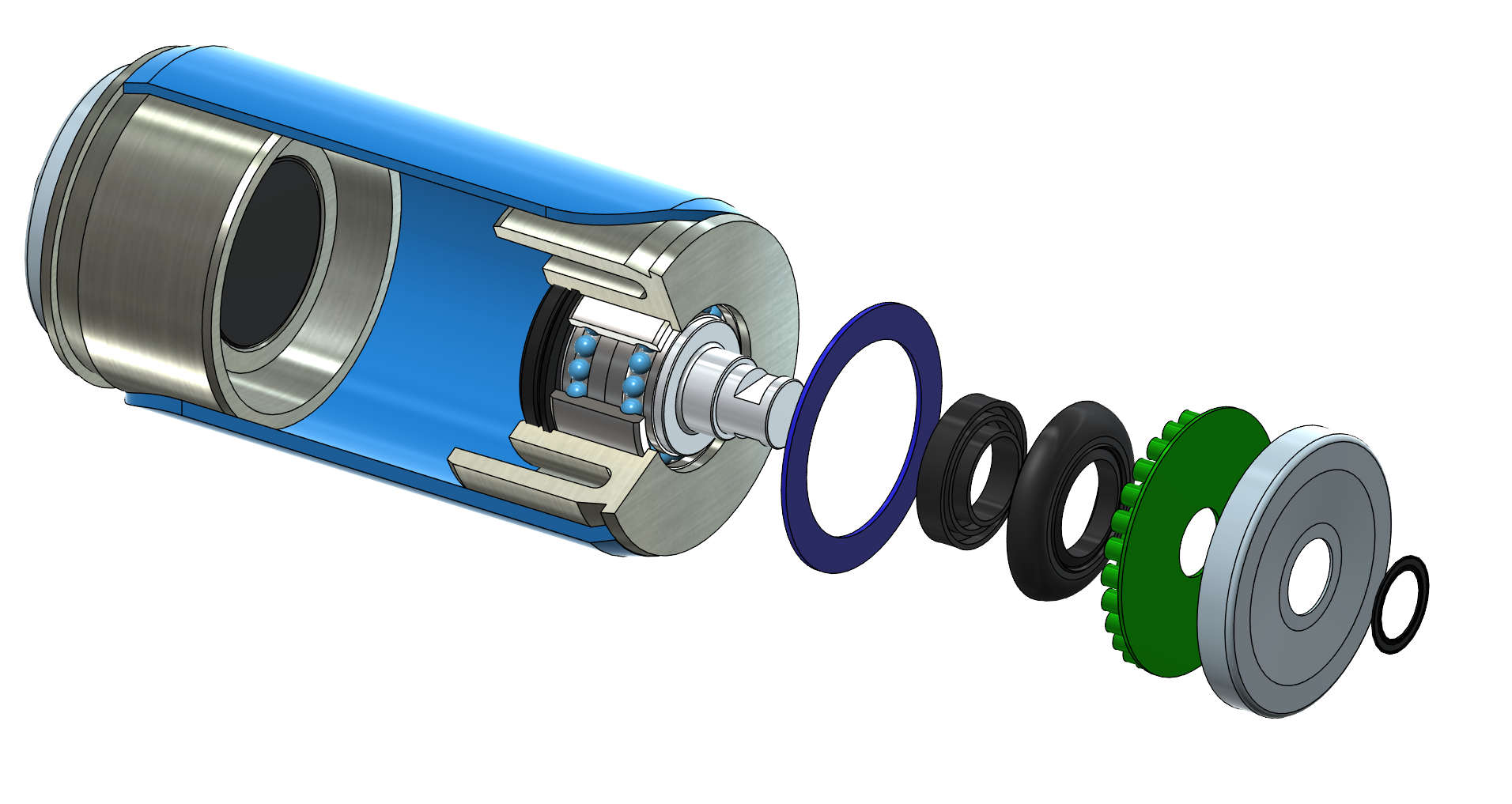
GEN 7
CII maintains a clear focus to partner with mining companies in the advancement of innovative conveyor technology. Our solutions has achieved significant cost savings that vastly benefit and improve performance standards in mining and industrial sectors.
CII . Conveyor Innovations International Pty Ltd is an Australian company that specialises in the design, manufacturing and supply of Conveyor Idler Rollers. Located in Emerald Queensland, with a manufacturing facility in Sydney.
CII’s current production roller is the Gen 7. The whole purpose of CII’s roller design has been to eliminate the causes of failure which are inherent in conventional rollers.
The benefit of using CII rollers is that mines and ports will use less rollers over time, which translates to increased production and significant cost savings.
Materials-handling conveyors are the life blood of mines and ports, moving on average around $400,000 – $1,100,000 of materials per hour. If a key conveyor stops as result of the failure of a conveyor idler roller, the whole operation can stop whilst the roller is replaced.
CII maintain a clear focus to partner with mining companies to advance the innovation of conveyor technology, achieving significant cost savings and vastly improved performance standards.
CII . APPS
SMART-APP CONVEYOR PRODUCTS – WORKING TOGETHER
Our research for conveyor idler rollers lead the development of the CII Roll App with advanced features designed to collect and record idler roll performance using a smart device such as an iPad. During the development phase we explored the process of detecting roller failure. This lead to the development of the smart Roller – iRoller. The heart of the iRoller is the iMonitor, a microelectronic device with accompanying firmware that can be fitted to a conventional roller such the Gen 7.
The iMonitor, is a Bluetooth device that is designed to automatically detect temperature, vibration, and operational hours. What it does, is send the information in real time to a controller, which then relays the information site control or the Cloud.
In addition to being able to monitor the information from an iRoller on a computer screen, we have developed a system using Microsoft HoloLens to enable mine personnel to monitor the whole conveyor system on a site in real time in a 3D Holographic environment.
This environment can be extended to the whole mine site or port so that the information can be viewed offsite, by management as a digital twin.
[1] Specialist CNC engineering products – e.g. shear pins for underground mining and idler rolls CII also has a wholly owned subsidiary Nogoa Engineering which specialises in refined CNC lathe products such as sheer pins for longwall miners and also pins for railway wagons.
CII . SOLUTIONS
WE WELCOME YOUR ENQUIRY – CALL US TODAY!
EXTENDED WARRANTY
CII provides a warranty of 3 years for Carbon Steel, and a warranty of 5 years on VitreSteel rollers. The extended warranty covers both bearings and shell wear. In extreme situations where the conveyors are not CEMA or Australian Standard compliant, the conveyors are reviewed on a case by case basis.
CII . ADVANTAGES
Advantages of our CII Rollers compared to conventional rollers:
BENEFITS OF USING CII ROLLERS
CII’s Gen 7 Rollers perform reliably, have greater load bearing capacity, a longer life than conventional rollers and are lighter for longer length rollers, where it counts.
Increased Productivity
Reduction of Unscheduled down time: CII Rollers by their design are robust, so this reduces their failure rate at site.
Improved Roller Life-force
Vastly decreases rate of critical conveyor failure or unscheduled shut-down. CII enforce longer length rollers, where it counts.
Extended Run Time
If a mine loses 2 hours in unscheduled down time a month this would equate to about $10,108,800 per annum. CII has greater load bearing capacity and a longer life.
Reduction in Mine Shuts
A well run conveyor enables a mine or port to extend its shut downs from 4 weeks to once every 8 to 12 weeks. Where a 24 hour shut down of a mine (conveyors travelling at 3,600 tonnes per hour) is extended from 4 to 8 weeks this will equate to 120,000 tonnes per shut and save the mine about $60.7 M p.a.
Savings on Roller Replacement
Our mine-stire surveys show a reduced number of rollers required over extended periods, resulting in significant cost savings. Over time we have reduced our clients’ large number roller requirements, their supply, delivery and installation – resulting in less downtime and increased productivity.
WARRANTY
Our replacement rate of rollers under warranty is about 0.82% per annum. The savings by using our rollers are significant. This means increased productivity, labour and replacement rollers cost overall. CII continue to develop technology to advance production, decrease costs, and increase efficiency. CII . The Future in Conveyor Innovations.
CII . TEL
07 . 4982 4814
CII . FAX
07 . 5575 2017
CII . EMAIL